Économie d'énergie dans l'entreprise - les principales directions:
- Économiser l'électricité
- Réduction des pertes de chaleur et de vapeur
- Réduction des pertes dans les lignes vapeur
Économie d'énergie dans l'entreprise - Méthodes d'économie d'énergie
- Sélection de la catégorie de prix optimale et révision des conditions contractuelles de fourniture
- Optimisation des moteurs électriques
- Installation VFD
- Optimisation des systèmes d'air comprimé
Choix de la catégorie de prix optimale pour l'alimentation
Au total, il existe 6 catégories de prix de l'électricité, dans lesquelles les entreprises peuvent acheter de l'électricité auprès de fournisseurs garantis.
Toutes les petites entreprises dont la puissance installée est inférieure à 670 kW, au moment de la signature d'un contrat d'alimentation électrique automatique, entrent dans la première gamme de prix.
Toutes les entreprises dont la puissance installée est supérieure à 670 kW entrent automatiquement dans la troisième catégorie de prix.
Les première et troisième catégories de prix ne sont pas toujours les catégories de puissance les plus optimales et les plus économiques.
Dans certains cas, le passage à une autre catégorie de prix peut réduire le coût de l'électricité de 5 à 30 %.
Le sujet des catégories de prix est assez large, dans notre examen des catégories de prix, nous expliquons en détail comment calculer et choisir correctement la catégorie de prix de l'alimentation.
En plus des catégories de prix, nous vous recommandons d'étudier également d'autres aspects du contrat d'alimentation :
- niveau de tension,
- Puissance,
- tarif de transport d'électricité.
Dans notre revue, vous pouvez découvrir ces méthodes et d'autres pour réduire les coûts énergétiques.
Économie d'énergie dans l'entreprise - Moteurs électriques
Il est nécessaire de prendre en compte tous les équipements dans lesquels des moteurs électriques sont utilisés :
- pompes,
- compresseurs,
- ventilateur,
- des machines-outils,
- lignes de production.
Plan de contrôle du moteur électrique
Le plan de contrôle du moteur doit devenir une partie intégrante du programme d'économie d'énergie de l'usine.
Ce plan permettra de mettre en place un système d'économie d'énergie à long terme pour tous les moteurs électriques de l'entreprise.
Le plan de vérification du moteur garantira qu'aucun défaut ni dysfonctionnement ne se produira, et s'ils se produisent, ils seront résolus rapidement et efficacement.
Étapes pour créer un plan de contrôle du moteur :
- Faire un inventaire de tous les moteurs de l'installation.
- Faites une liste des moteurs avec leurs principaux paramètres, conditions techniques, durée.
- Élaborer des instructions générales pour effectuer des réparations.
- Élaborer des directives pour l'entretien préventif, la lubrification et l'inspection.
- Créez un stock sûr de pièces détachées fréquemment utilisées.
- Créez une spécification d'achat pour les nouveaux moteurs.
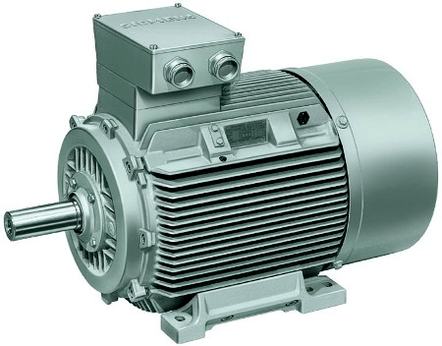
Rebobinage de moteurs électriques
En règle générale, le rembobinage d'un vieux moteur électrique est beaucoup moins cher que d'en acheter un nouveau.
Le moteur électrique doit être remplacé si le coût du rebobinage est supérieur à 60% du coût d'un nouveau.
Donc tout dépendra de la façon dont le rembobinage est fait.
Si le travail est effectué au plus haut niveau, le moteur ne perdra que 1% -2% de son efficacité.
Si le rembobinage est mal effectué, les pertes dans le moteur électrique augmenteront de 5% -10%.
Remplacer l'ancien moteur électrique par un nouveau, économe en énergie, est logique dans les cas où le moteur fonctionne plus de 2000 heures par an.
La période d'amortissement d'un nouveau moteur écoénergétique ne dépassera pas 1, 5 à 2 ans.
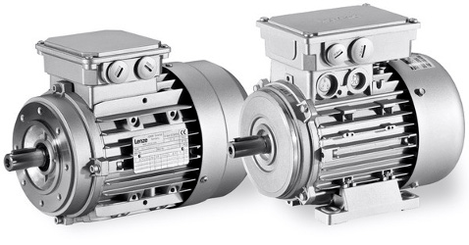
Économie d'énergie dans l'entreprise en augmentant le facteur de charge
Le facteur de charge est le rapport entre la puissance de fonctionnement et la puissance apparente.
C'est ainsi que l'énergie est utilisée efficacement.
Plus le facteur de charge est élevé, plus l'utilisation de l'électricité est efficace.
Le moteur électrique fonctionne de manière optimale avec une charge de 75 % et plus.
Par conséquent, l'installation de moteurs au-dessus de la puissance requise (pour des raisons de sécurité) sera non seulement plus coûteuse, mais également inefficace en termes de consommation d'énergie.
Le facteur de charge peut être augmenté comme suit :
- arrêt des moteurs épuisés,
- remplacement des moteurs, avec une charge inférieure à 45%, pour les modèles moins puissants,
- redistribution de la charge entre les moteurs électriques existants.
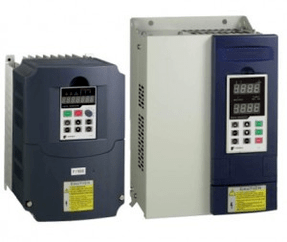
Convertisseur de fréquence (VFD)
L'installation de convertisseurs de fréquence n'a de sens que pour les systèmes dynamiques.
Dans les systèmes statiques, qui ne sont impliqués, par exemple, que pour le levage de charges, l'installation d'un convertisseur de fréquence n'aide pas et peut souvent causer des dommages.
Le VFD équilibre la charge et la vitesse du moteur, garantissant ainsi que l'énergie électrique est utilisée de manière optimale.
Le VFD peut réduire la consommation d'énergie du moteur d'un minimum de 5 % et d'un maximum de 60 %.
La période de récupération du VFD est généralement de 1 à 3 ans.
Optimisation des systèmes d'air comprimé
L'air comprimé est utilisé dans une grande variété d'industries.
Dans certaines entreprises, l'air comprimé est le principal consommateur d'électricité.
L'air comprimé est utilisé dans les dispositifs et équipements pneumatiques, sur les bandes transporteuses, les lignes automatiques.
L'utilisation de l'air comprimé est populaire car c'est une source d'énergie pratique et sûre.
Mais beaucoup de gens oublient que l'air comprimé est l'une des sources d'énergie les plus inefficaces : seulement 5 % de l'électricité dépensée pour produire de l'air comprimé se transforme en travail utile, les 95 % restants vont dans le tuyau.
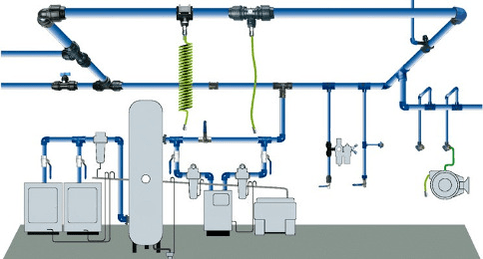
Économie d'énergie dans l'entreprise - air comprimé :
- Ne pas utiliser d'air comprimé pour nettoyer les locaux.
- Réduire la température de l'air à l'entrée du compresseur de 3 % réduit la consommation d'énergie de 1 %.
- Pour ces processus techniques, dans la mesure du possible, minimisez la pression d'air comprimé. Baisser la pression de 10 % réduit la consommation d'énergie de 5 %.
- Effectuer des inspections régulières, des réparations des équipements de compresseurs et des lignes de transmission d'air comprimé. Une, même la plus petite perte d'air comprimé, peut parfois réduire l'efficacité de l'équipement.
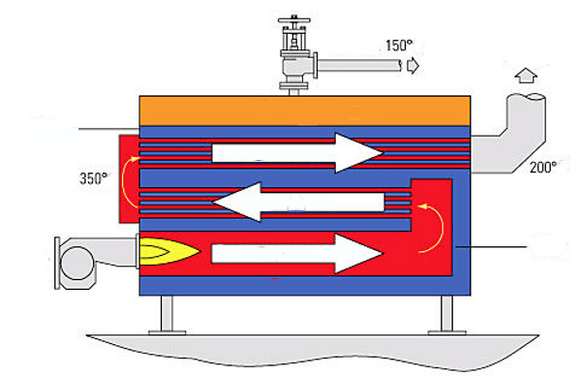
Économie d'énergie dans l'entreprise : nous réduisons les pertes de chaleur et de vapeur
La vapeur est souvent utilisée dans l'industrie, en particulier dans les industries du textile, de l'alimentation et de la transformation.
L'amélioration de l'efficacité des chaudières à vapeur et la réutilisation de la chaleur générée peuvent réduire considérablement la consommation d'énergie de ces systèmes.
Production de vapeur
La chaudière fonctionne plus efficacement à pleine puissance.
Du fait que la demande de quantité de vapeur peut varier dans le temps, il arrive souvent que la chaudière fonctionne en dessous de sa charge optimale.
La capacité de la chaudière installée peut être bien supérieure aux besoins de l'entreprise, en raison d'une baisse de la demande de produits ou de plans non réalisés pour augmenter la production.
De plus, la capacité de la chaudière peut ne pas être requise en raison d'améliorations du processus de production ou de l'introduction de mesures d'économie d'énergie.
Dans de tels cas, la chaudière fonctionne soit pas à pleine capacité, soit en mode cycle court marche-arrêt.
Ces deux situations entraînent des pertes d'énergie importantes.
Il n'existe pas de solutions simples et peu coûteuses à ce problème.
L'option la plus simple estinstaller une "petite" chaudière qui fonctionnera à pleine capacitéà une charge de travail moyenne ou faible dans l'entreprise.
Bien que ce ne soit pas une solution économique, la période de récupération d'un tel investissement peut être inférieure à deux ans.
Et, en général, il est de plus en plus efficace d'avoir plusieurs petites chaudières interchangeables, en particulier dans les entreprises avec une demande changeante ou des fluctuations saisonnières importantes de la consommation de chaleur et de vapeur.
Système de réglage automatique
Si l'entreprise possède plusieurs chaudières, il est logique de l'installersystème de régulation automatique de charge de chaudière. . .
L'automatisation répond au besoin de vapeur dans l'entreprise, en redistribuant la charge entre les chaudières, en allumant ou en éteignant les chaudières, augmentant ainsi considérablement l'efficacité de l'ensemble du système.
Robinet-vanne
Dans les entreprises où les chaudières sont régulièrement éteintes en raison d'une baisse de la demande de vapeur, les pertes de chaleur par la cheminée peuvent être assez élevées.
Il est possible de bloquer la perte d'air chaud par la cheminéeen installant un robinet-vannequi ferme le tuyau lorsque la chaudière est éteinte.
Prévention et entretien
S'ils sont laissés sans surveillance, les brûleurs et les systèmes de retour de condensat peuvent rapidement se détériorer ou tomber en panne.
Cela peut réduire l'efficacité de la chaudière de 20 à 30 %.
Un programme de maintenance simple - garantissant que tous les composants de la chaudière fonctionnent au plus haut niveau - augmentera considérablement l'efficacité opérationnelle.
En pratique, un entretien régulier permet de réduire de 10 % la consommation énergétique de la chaudière.
Isolation : la perte de chaleur de la surface d'une chaudière correctement isolée doit être inférieure à 1 %.
Élimination de la suie et des incrustations
Il est nécessaire de surveiller et d'éliminer en permanence la formation de suie sur les tuyaux de la chaudière, le tartre à l'intérieur de la chaudière.
Une couche de suie de 0, 8 mm d'épaisseur réduit le transfert de chaleur de 9, 5 %, tandis qu'une couche de 4, 5 mm d'épaisseur réduit le transfert de chaleur de 69 % !
L'encrassement se forme lorsque le calcium, la magnésie et le silicium se déposent sur l'échangeur de chaleur de la chaudière.
L'échelle de 1 mm d'épaisseur augmente la consommation d'énergie de 2%.
La suie et les incrustations peuvent être éliminées mécaniquement ou avec des acides.
La formation de suie et de tartre peut être déterminée par une augmentation de la température des fumées ou par un contrôle visuel lorsque la chaudière n'est pas en fonctionnement.
La formation de suies et d'incrustations doit être surveillée avec une attention particulière si la chaudière fonctionne avec des combustibles solides (charbon, tourbe, bois de chauffage).
Les chaudières à gaz sont moins sujettes aux problèmes de suie.
Optimisation de la purge des chaudières
La purge de la chaudière est le drainage de l'eau de la chaudière pour nettoyer l'eau à l'intérieur de la chaudière des impuretés et des sels.
Le but de la purge de la chaudière est d'éviter ou de réduire la formation de tartre.
Une purge insuffisante de la chaudière peut entraîner une entrée d'eau dans la vapeur ou la formation de dépôts dans la chaudière.
Une purge excessive signifie une perte de chaleur, d'eau et de produits chimiques.
Le niveau de purge optimal dépend du type de chaudière, de la pression de service dans la chaudière, de la préparation et de la qualité de l'eau utilisée.
La première chose à laquelle il faut faire attention est la préparation de l'eau. Si l'eau est bien traitée (faible teneur en sel), le taux de purge peut être de 4 %.
S'il y a des substances étrangères et des sels dans l'eau, le taux de purge sera de 8% -10%.
Le système de purge automatique peut également réduire considérablement la consommation d'énergie.
La période de récupération d'un tel système est généralement de 1 à 3 ans.
Réduction des émissions de fumée
Un excès de fumée est souvent le résultat de l'entrée d'air dans la chaudière et la cheminée par des fuites et des ouvertures.
Cela réduit le transfert de chaleur et augmente la charge sur le système de compression.
Les fuites et les trous peuvent être facilement éliminés, il suffit d'effectuer périodiquement une inspection visuelle de la chaudière et de la cheminée.
Régulation de l'air
Plus on utilise d'air pour brûler du carburant, plus la chaleur est projetée dans le vent.
Une quantité d'air légèrement supérieure au rapport stoechiométrique idéal carburant/air est nécessaire pour des raisons de sécurité, pour réduire les émissions de NOx, et dépend du type de carburant.
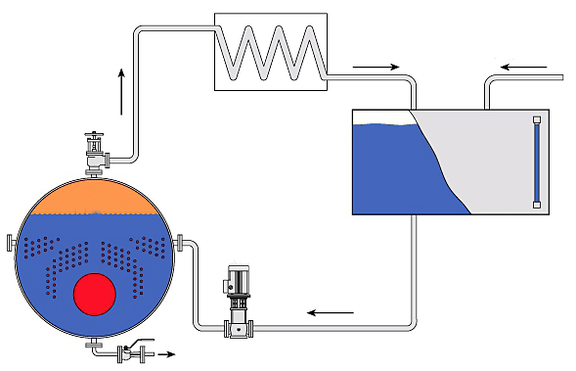
Les chaudières en mauvais état technique peuvent utiliser jusqu'à 140 % d'air en plus, ce qui entraîne des émissions de fumées excessives.
Un brûleur à gaz efficace nécessite 2 à 3 % d'oxygène supplémentaire ou 10 à 15 % d'air supplémentaire pour brûler le combustible sans générer de monoxyde de carbone.
La règle générale est que le rendement de la chaudière augmente de 1 % pour chaque 15 % de réduction d'air supplémentaire.
Par conséquent, il est nécessaire de vérifier en permanence le rapport carburant / air.
Cet événement ne coûte rien, mais il a un grand effet.
Surveillance des émissions de fumée
La quantité d'oxygène dans les fumées est la somme de l'air supplémentaire (ajouté pour augmenter la sécurité et réduire les émissions) et de l'air qui s'infiltre dans la chaudière par les trous et les fuites.
La présence de fuites et de trous peut être facilement détectée si un système est mis en place pour surveiller l'air entrant et la quantité d'oxygène dans les fumées.
En utilisant des données sur la quantité de monoxyde de carbone et d'oxygène, il est possible d'optimiser le rapport combustible/air dans la chaudière.
L'installation d'un système de surveillance et d'analyse des émissions de fumée s'amortit généralement en moins d'un an.
Économie d'énergie dans l'entreprise - Installation d'un économiseur
La chaleur des fumées peut être utilisée pour chauffer l'eau qui entre dans la chaudière.
L'eau chauffée pénètre dans la chaudière et nécessite moins de chaleur pour être convertie en vapeur, économisant ainsi du carburant.
Le rendement de la chaudière augmente de 1 % pour chaque baisse de 22 °C de la température des fumées.
L'économiseur peut réduire la consommation de carburant de 5 à 10 % et s'amortit en moins de 2 ans.
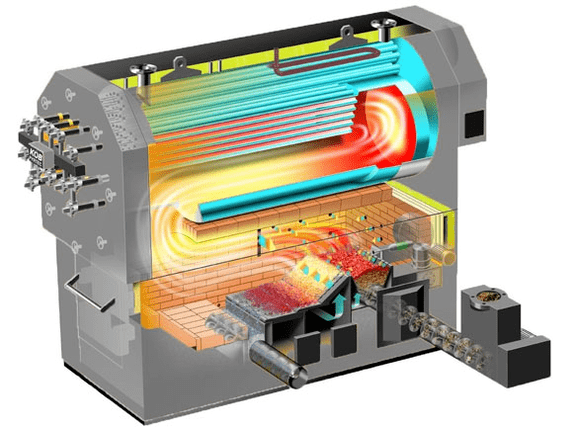
Échangeur de chaleur pour extraire la chaleur de l'eau et la vapeur de la purge de la chaudière
L'échangeur de chaleur aidera à recycler environ 80 % de la chaleur de l'eau et de la vapeur provenant de la purge de la chaudière.
Cette chaleur peut être utilisée pour chauffer des bâtiments ou pour chauffer l'eau qui alimente la chaudière.
Toute chaudière avec un taux de purge constant de 5% ou plus est un excellent candidat pour un échangeur de chaleur.
Si le système de purge ne fonctionne pas en mode constant, il est judicieux d'envisager de le passer en mode constant tout en installant un échangeur de chaleur en même temps.
La période d'amortissement moyenne d'un échangeur de chaleur ne dépassera pas 1, 5 à 2 ans.
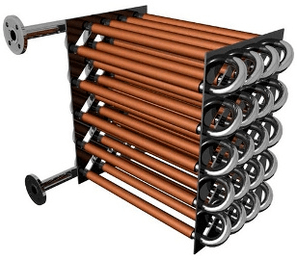
Installation d'un économiseur à condensation
Les condensats chauds peuvent être renvoyés dans la chaudière, économisant ainsi de l'énergie et réduisant le besoin d'eau traitée.
L'économiseur à condensation peut augmenter l'efficacité du système de 10 % supplémentaires.
L'installation d'un tel économiseur doit être effectuée sous la stricte supervision de spécialistes qui prendront en compte toutes les nuances d'un tel système, son effet sur la chaudière et la composition chimique de l'eau.
L'utilisation d'un système qui renvoie les condensats à la chaudière s'amortit généralement en 1 à 1, 5 an.
Un système qui dirige les condensats vers une alimentation en eau chaude s'amortit en moins d'un an.
<10_img_centerxx>Tours de refroidissement (tours de refroidissement)
Une tour de refroidissement est un échangeur de chaleur dans lequel l'eau est refroidie par un courant d'air.
Et en termes d'efficacité énergétique, une tour de refroidissement est un appareil qui rejette de la chaleur dans le vent.
Potentiel d'économie d'énergie dans les tours de refroidissement :
- Dans certaines entreprises, il est logique de s'éloigner complètement des tours de refroidissement. Il existe de nombreux cas où le chauffage est utilisé pour chauffer une pièce et en même temps une tour de refroidissement est utilisée pour dissiper la chaleur. L'installation d'une pompe à chaleur résoudra le problème de chauffage et réduira au moins partiellement le besoin d'utiliser la tour de refroidissement.
- L'installation de disjoncteurs pour les ventilateurs des tours de refroidissement peut réduire la consommation d'énergie de 40 %.
- Le remplacement des ventilateurs en aluminium ou en fer par de nouveaux (moulés en fibre de verre et en plastique) peut réduire la consommation d'énergie jusqu'à 30 %.
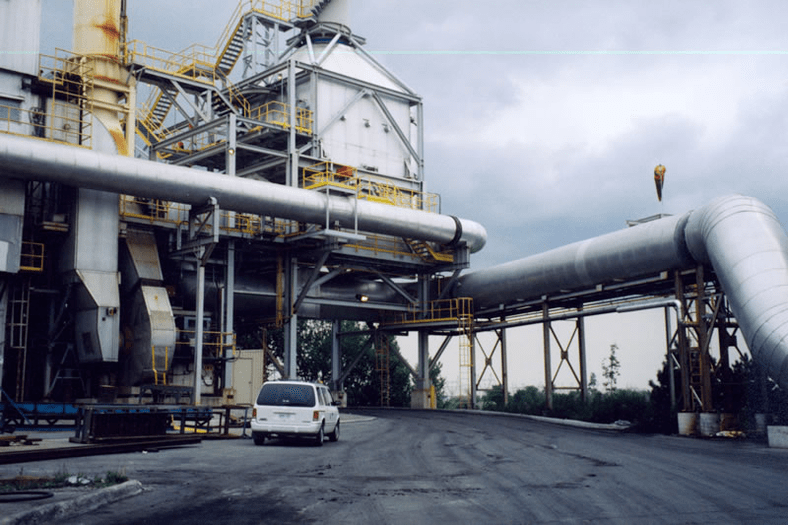
Réduction des pertes dans les lignes vapeur
Déconnexion des conduites de vapeur non réclamées
Les besoins et la consommation de vapeur sont en constante évolution.
Cela peut conduire au fait que l'ensemble du système de distribution de vapeur n'est pas utilisé à pleine capacité, mais seulement à 20% -50%, ce qui entraîne inévitablement des pertes de chaleur.
Il est clair que l'optimisation ou la reconfiguration de l'ensemble du système de distribution de vapeur pour répondre aux nouveaux besoins sera très coûteuse et peut-être pas réalisable.
Cependant, l'identification et la fermeture des conduites de vapeur sous-utilisées peuvent être une mesure d'économie d'énergie très efficace.
Économie d'énergie dans l'entreprise - Isolation thermique des tuyaux
L'isolation des tuyaux de vapeur peut réduire les pertes d'énergie jusqu'à 90 %.
C'est l'un des retours d'économies d'énergie les plus rapides dans un système de distribution de vapeur.
Le délai moyen de retour sur investissement pour l'isolation des canalisations par lesquelles la vapeur ou l'eau chaude est transmise est d'environ 1 an.
Condensats tuyaux pour 1, 5-2 ans.
Surveillance des drains de condensats
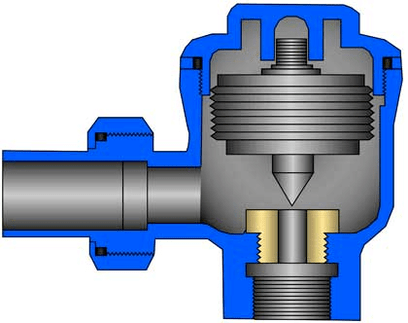
Un programme simple pour surveiller l'état technique des purgeurs de vapeur peut réduire considérablement les pertes de chaleur.
Par exemple, si la maintenance n'est pas effectuée pendant 3 à 5 ans, généralement environ un tiers des purgeurs de vapeur sont hors service, permettant à la vapeur d'entrer dans le système d'évacuation des condensats.
En pratique, dans les entreprises disposant d'un programme de surveillance des purgeurs, pas plus de 5 % des purgeurs ne sont en panne.
La période d'amortissement moyenne pour le remplacement ou l'entretien d'un purgeur de vapeur est inférieure à six mois.
Un programme de surveillance des purgeurs réduira généralement les pertes de vapeur de 10 %.
Purgeurs thermostatiques
L'utilisation de purgeurs thermostatiques modernes peut réduire la consommation d'énergie tout en augmentant la fiabilité de l'ensemble du système.
Le principal avantage des purgeurs thermostatiques est qu'ils
- ouvert lorsque la température approche du niveau de vapeur saturée (+/- 2 C°),
- émettre des gaz non condensables après chaque ouverture e
- ils sont à l'état ouvert au début du fonctionnement du système, ce qui assure son échauffement rapide.
De plus, ces purgeurs de vapeur sont très fiables et peuvent être utilisés sur une large gamme de pressions.
Déconnexion des drains de condensats
La consommation d'énergie peut être réduite en fermant les purgeurs de vapeur sur les conduites de vapeur surchauffée lorsqu'ils ne sont pas utilisés.
Élimination des fuites de vapeur
Un programme de réparation de fuites de vapeur de petits trous peut être rentable en moins de 3 à 4 mois.
Il ne faut pas oublier que de petites fuites peuvent passer inaperçues pendant des années, endommageant constamment le système.
Réutilisation des condensats et de la vapeur
Lorsqu'un purgeur évacue le condensat d'un système à vapeur, la chute de pression crée de la vapeur à partir de ce condensat.
Cette vapeur, avec le condensat, peut être utilisée dans un échangeur de chaleur pour chauffer l'eau d'alimentation ou l'air.
Plus important encore, il est possible d'utiliser cette vapeur et ce condensat près du point de rejet, car il peut être très coûteux de créer un système de tuyauterie séparé pour le transporter jusqu'au point d'utilisation.